Putting the coast of Maine back together will take know-how and patience. After two back-to-back, record-breaking storms in Maine, there may not be any getting back to normal. According to a webinar offered by the Island Institute in Rockland, Maine, normal is over.
The Gulf of Maine has risen 7.5 inches in the last hundred years, and that rate is expected to increase, with a rise of 1.5 feet in the next 26 years. Things are expected to get worse and the public and private owners of the coastal infrastructure that needs rebuilding are getting the message. “We need to overbuild,” says Mark Zaccadelli, Ocean’s Edge Marine Construction owner in Bristol, Maine.
The waves have laid down, the storm surge has receded, and slowly, on the coast of Maine, fishermen and wharf owners are coming to terms with the challenges of rebuilding.
“As I understand it the DEP [Maine Department of Environmental Protection] will let people rebuild piers and shoreside stabilization on the original footprints. And they can raise the piers by four feet,” says Zaccadelli. “Right now, it you rebuild on the original footprint, you can get a permit by rule, which takes two weeks. But if you make changes, like raising the height, it usually requires an NRPA, which can take six months to a year, and you have to work with the DEP and the US Army Corps of Engineers.”
On permitting, Zaccadelli has found the process so time-consuming that he contracts it out to Gartley & Dorsky, an engineering and surveying firm in Camden, Maine. But the Maine Legislature’s Environmental Committee voted in favor of the fast-track permit by rule process for wharf owners who want to build stronger structures.
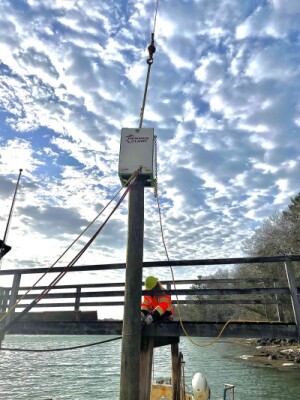
Zaccadelli was fully booked before the storms and now he’s helping people get their bearings on where to go.
“I’m getting calls,” he says. “People are trying to figure out what to do. The days of driving piles with a backhoe or pushing them in with a crane are over. We have a pneumatic pile driver that can get pilings down to the clay, the hardpan that’s going to hold them, and that’s what has to be done now.”
Zaccadelli has looked at some wharves that need to be rebuilt, and where necessary, he is advising owners to start from scratch. “We can pull or jet out older pilings that are not going to last, and we have to rethink the bracing,” he says, noting that trying to save a dollar could end up costing more if storms like January’s are truly the new normal.
“I like to think my rates are reasonable,” says Zaccadelli. “Marine construction is a different beast than construction on land. You have wind and tide to deal with.” Not to mention often working blindly. “A lot of the coast is a ledge,” he points out. “From the low water up, we can drill and pin pilings, but in deeper water, it gets more difficult.”
Zaccadelli notes that the high cost of hiring a well-equipped marine construction company like his, or Prock Marine Company in Rockland, or several others, not to mention their limited availability, will compel many people to do their own work.
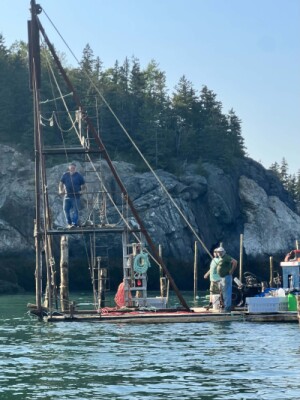
He believes the pile drivers used Downeast for building herring weirs could do a reasonable job. “Those are similar to what I have, just slower. As long as you’re getting a 1/4 inch of movement with each hit, keep going. I usually do ten more drops when I see no movement, just to make sure you’re not up against a rock or somthing.”
Zaccadelli recommends southern yellow pine for pilings. “Or steel, though that requires maintenance. But the oak days are over,” he says.
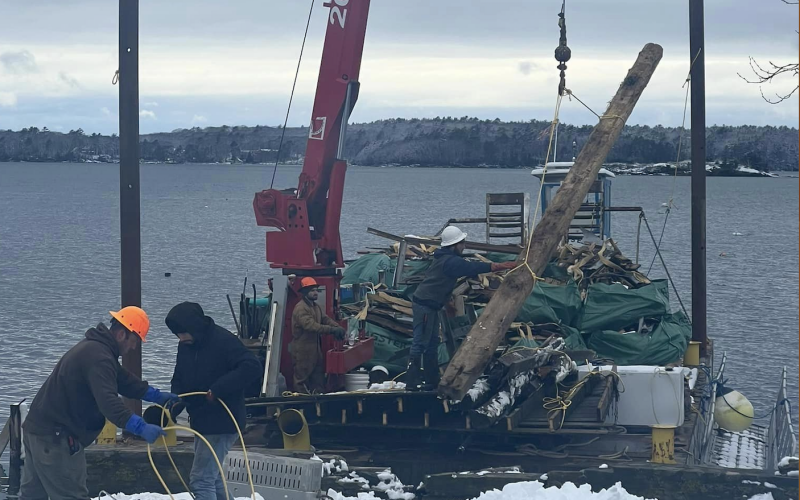
It's clear, based on the messaging coming from the Department of Marine Resources, the science being presented by the Island Institute, and what Zaccadelli point out is common sense, that Maine needs to build back stronger in order to have a resilient working waterfront. But with inflation and a high demand for material and workers, especially skilled workers, the rebuild will obviously cost more.
While many wharf owners want to build back quickly, many foresee a lot of ‘skiffing.’
“You know, fishermen will have to load all their product and things into a skiff to land it,” says Amity Chipman of Chipman’s Wharf in Milbridge.
According to Gabrian McPhail of Resilient Communities on Vinalhaven, there is funding available, but primarily for the public sector. For example, Governor Janet Mills has proposed using $50 million from the state’s rainy-day fund to help communities rebuild, and federal money may be coming.
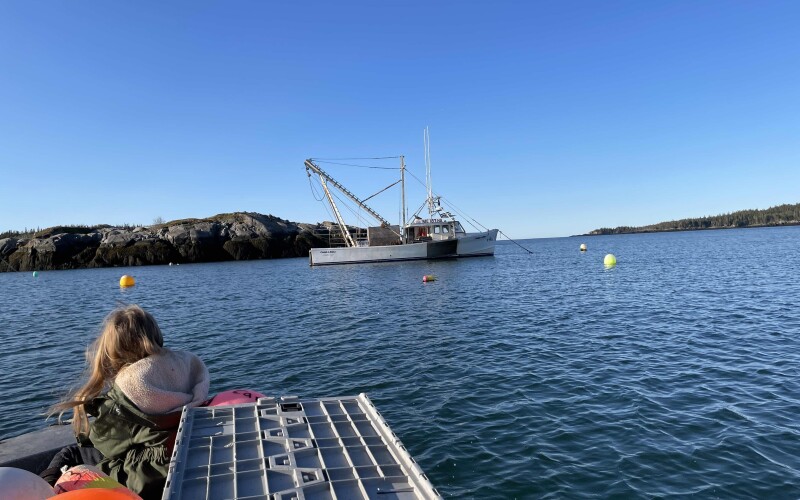
“I’m less familiar with private sector funding sources that are short-term, response-type options,” says McPhail. “Business grant programs and low-interest loans through USDA and the Economic Development Administration are longer term funding mechanisms. Long term public funding options that can also benefit private infrastructure are FEMA Hazard Mitigation Grants.”
McPhail suggest that one way for private companies to learn about available funding is to contact their regional planning organization, which she believes should be able to talk to them about funds that it administers or connect them to more information and resources. She adds this link to all the regional planning organizations in the state:
“You can also add the Sunrise County Economic Council to that list,” McPhail says. “The Island Institute also has a list of financial resources for rebuilding the working waterfront. As does the Maine Coast Fishermens’ Association and the DMR.
So far the Island Institute has awarded 14 grants of up to $5,000 to working waterfront businesses that in total impact, 96 full-time employees, 102 part-time employees, and more than 640 fishing boats or aquaculture operators who rely on these facilities. These grants are a drop in the bucket of what will be needed, but they’re a start.