One indicator of the health of a fishery is the number of new boats being built for it, and design trends of those boats add more to the story. North Pacific fisheries journalist and author Peter Marsh estimates that between West Coast and Alaska boatbuilders, somewhere close to 30 new gillnetters will enter the healthy Bristol Bay salmon fishery in 2021.
“And this is a slow year, due to the pandemic,” he says.
Tom Farrell, of Farrell and Norton Naval Architects in Maine, is busy designing scallopers for the lucrative Atlantic scallop fishery. A number of his and his partner Garrett Norton’s boats have arrived in New Bedford in recent years, and more are coming.
For decades, the lobster industry has sustained fishing communities on the coast of Maine, and Moses Ortiz, owner of Boricua Custom boats in Harrington, Maine, has fitted out numerous hulls for that fishery. But as climate change and markets create uncertainty for lobsters, fisherman Dean Barrett is having Ortiz build a boat for lobstering and scalloping.
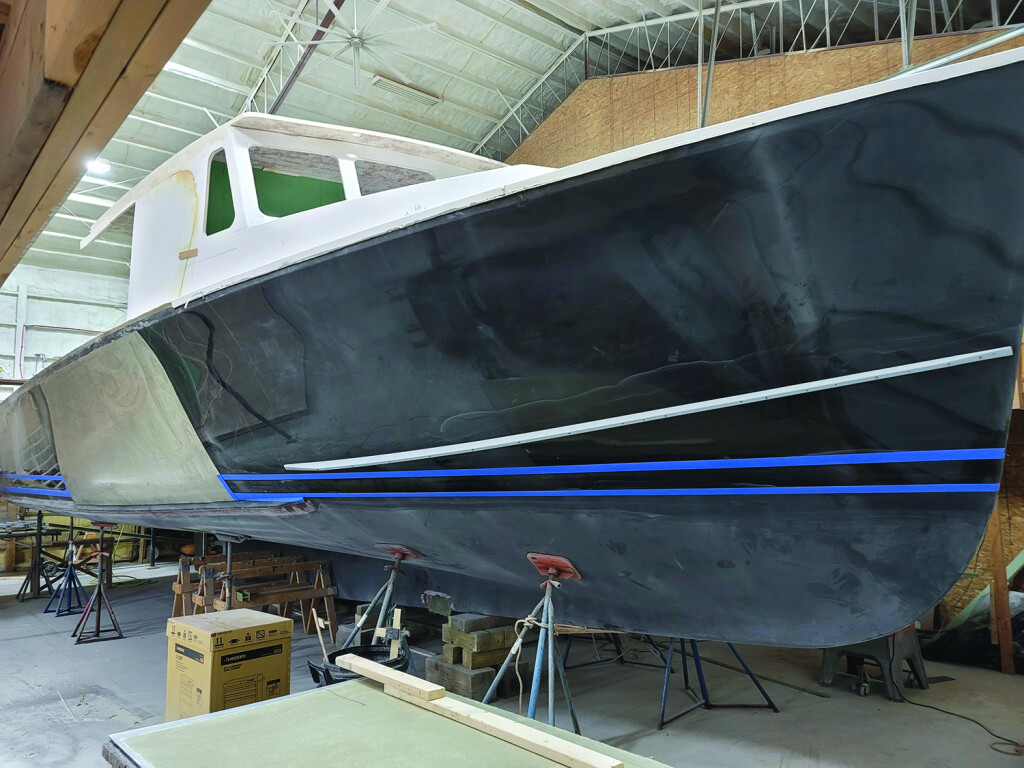
“Dean is a really hard-working fisherman,” says Ortiz. “He lobsters, and then goes scalloping down in Massachusetts.” Ortiz is fitting out Barrett’s boat to make it more efficient in both fisheries. “This boat is one of a kind. It started as a 47-foot Osmond [Beal]. H&H chopped it down to 44, and I made it 48.” According to Ortiz, the boat’s 1,000-hp MAN engine had the wrong gear. “It was 1.9, supposed to be 2.2.” Ortiz has strengthened the boat for mounting an A-frame and winch.
“We’re ready to mount the winch,” says Ortiz. “It’s pretty much a plug and play system. It came from Billings in Stonington. Lonnie’s Hydraulic set up the hydraulics system.”
The Atlantic scallop fishery is a lifeline for small boats looking to diversify, and 200-pound-per-day permits for the northern Gulf of Maine are selling for upward of $80,000. Newbuilds for the general category fleet, primarily out of New Bedford, have led to many innovations. One of the most interesting is the use of wing stabilizers, as seen in the NF May ’21 story on the F/V Heritage.
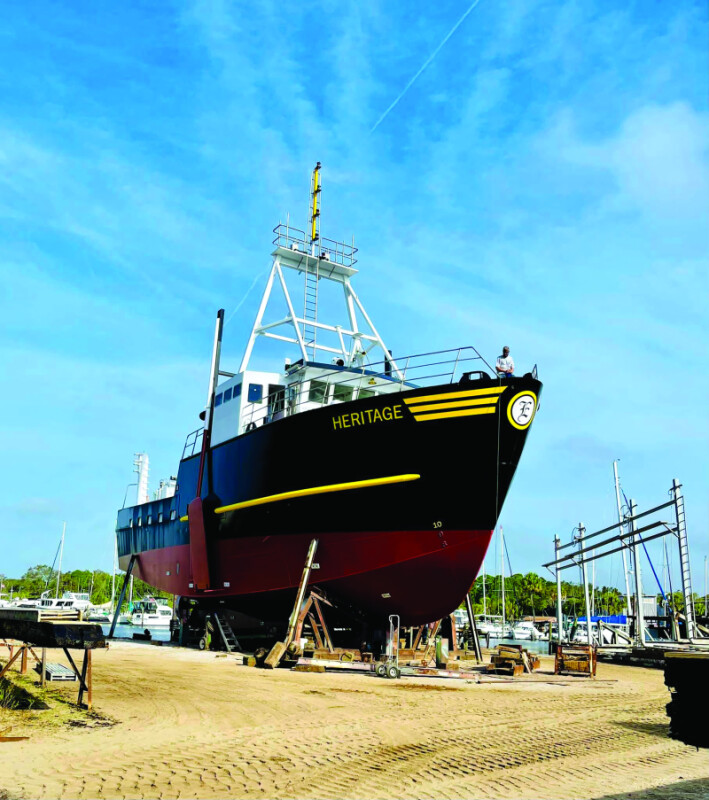
“They’re very popular. We’re putting them on a few boats in the scallop fishery, and we put them on a clam boat in New Jersey, the Christi Caroline,” says Farrell.
Dorchester Shipyard in New Jersey added the stabilizers to the 55-year-old Christi Caroline, which was rebuilt in 2017-18 at Boconco in Bayou La Batre, Ala., returning to service after a 13-year hiatus.
“What happened was she caught fire and made it back to port on December 2, 2005,” says Tom Dameron, fisheries liaison for the vessel owner Surfside Foods. “We basically took her down to the keel and built a new boat on top of her.” The new Christi Caroline, 124.5 feet long, 32 feet wide, with an 11-foot draft, is built on a mere 8 feet, 9 inches of the original. She made her first clamming trip in September 2018, and the wing stabilizers were added in 2019.
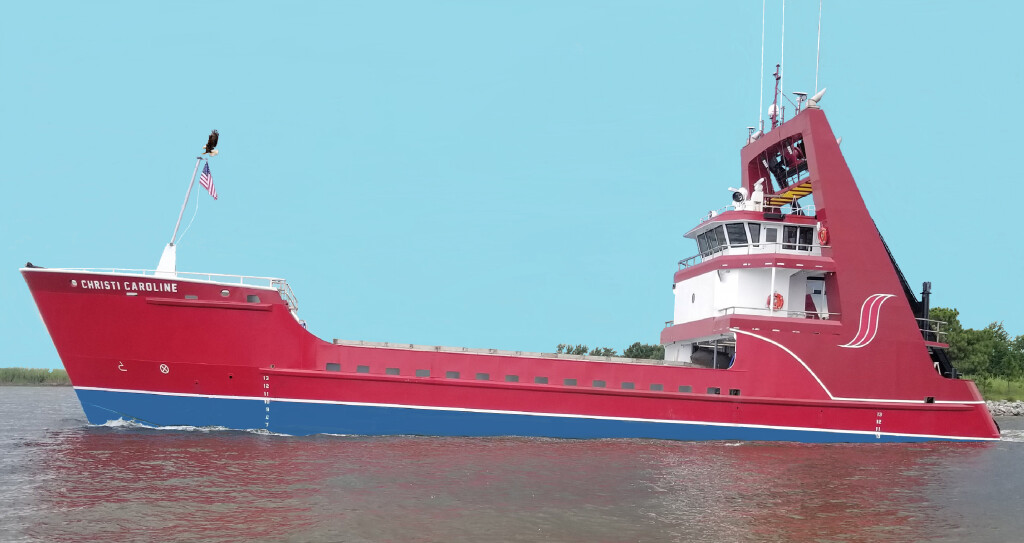
“We saw some done at Fairhaven Shipyard and thought we would give them a try,” says Dameron. “From what I hear, the guys really like them.”
Stephane Loubert, owner of Marinexpert Plus in Gaspe, Quebec, has designed most of the wing stabilizers for Farrell and other naval architects.
“I did my first one for the Fundy Leader, which was launched in 2006. Since then, I’ve done around 500. About 95 percent of the boats around here have switched from paravanes to wings. If they’re forward on the hull, they can help control the pitch, too.” Loubert has designed wings for 15 boats in the United States, so far. “The first one was the Iron Maiden, in Boston,” says Loubert. “Sometimes we send the files to the yards, but on six or seven, we put them together here and sent them.”
With the wings folded up in port, Loubert notes that they have to be protected. “We fabricate protectors, steel triangles that stick out from the hull on each side of the wing, or you can use those big balls. If you’re building new, you can add a place for them to fit into the hull when they are up.”
Among the advantages of the wing stabilizers that Loubert touts is fuel savings. “Our customers tell us that they lose half a knot with the wings down. They say with paravanes, they lose a knot.”
Farrell agrees that while healthy fisheries lead to new boats being built, so does an aging fleet. “We’re also working on a couple of draggers, because at a certain point you have to replace these boats.”
While hybrid power is another innovation getting attention from fishermen and architects, so far, the boats Farrell is designing are all diesel. “It’s coming, though,” he says. “Electric systems used to be too expensive, but now the price is getting so it is becoming a viable option.”
On the West Coast, the 184-foot longliner Northern Leader splashed in 2013 with a hybrid Z-drive system.
“They saved $500,000 in fuel the first year. So their payback for going diesel-electric was four to five years,” says Jonathan Parrott, of Jensen Maritime, designers of the vessel. “If they had batteries, the capital costs would be higher, but the savings would be even greater.” Since then, however, no other new big boats have gone hybrid. Parrott reports no new orders for hybrid powered commercial fishing vessels.
“Most of the action is in tugs. We are currently working on a fully electric tug for SoCal, it has generators aboard, but only for long-distance travel. The batteries will supply power for day-to-day work, for the most part. There is talk of fuel cells, but that entails some type of fuel — either hydrogen, LNG, methanol or ammonia, or something similar.”
Big boats may not be opting for hybrid systems, but there is some action in the small boat fleet. Contrasting with the sophistication of the engineering that went into the Northern Leader, Fabian Grutter of Sitka, Alaska, combined an improvised electric power system with the 350-hp John Deere on his 34-foot boat, the Sunbeam. “I melted the batteries,” says Grutter of his initial efforts, but he persisted. “I bought another 10 70-kilowatt batteries that I had made in China,” he says. “And a new BMS [battery management system]. It’s all working now. It saves me about 15 percent when I go out on long trips for halibut and blackcod, about 80 percent when I’m gillnetting close to home.”
Grutter’s idea has caught on with other small-boat owners. Eric Jordan and Kent Barkhau of the Alaska Longline Fishermen’s Association are reportedly preparing to go hybrid.
“They’re committed,” says Chandler Kemp, owner of Kempy Electronics in Sitka. “We’re applying for grants to help fund switching to hybrid systems.” According to Kemp, the fishermen are in talks with the Italian company Transfluid for purchasing turnkey systems.
“Transfluid has a unit that goes between the engine and the gear,” says Kemp. “It allows you to switch from diesel to electric, and allows the engine to charge the batteries and the electric motor to help the engine.”
With batteries and motor included, the Transfluid system costs as much as $150,000, Kemp notes, and he is not sure about the payback. “I don’t think you can pay it back on fuel savings alone,” he says. “Maybe if you include reduced maintenance and longer engine life. But there’s pay-offs in noise reduction.”
Fabian Grutter’s 4-year-old son agrees. “When I have him on the boat and start up the diesel, he covers his ears and tells me to turn on the little motor.”
In Alaska’s Bristol Bay, many fishermen are moving in the other direction, and are breaking the 1,000-hp barrier with twin installs of bigger engines. According to Mike Fourtner, commercial sales manager at Cummins, the company is putting twin 600-hp Cummins QSC 8.3 liter engines in dozens of Bristol Bay boats.
“The boats are limited to 32 feet,” says Fourtner. “But they’ve gotten wider, a lot of them are now 17 feet, and that has increased the weight from around 20,000 pounds to 30,000. So they need the power.” That power is now available in smaller footprint engines, Fourtner points out, and it’s making boats much faster. “In the old days, if you went 12 knots, that was normal,” he says. “Now our boats are going over 40 knots. If you are faster than the other guy it could be the difference between a $20,000 day and a $4,000 day.”
Dirk Rozema, owner of Rozema Boatworks in Mount Vernon, Wash., has built two 17-foot-wide Bristol Bay through-pickers for the 2021 season, both equipped with twin 600-hp Cummins engines, ZF gears and UltraJet 340 jets.
“The goal is to get up to speed and plane with 10,000 pounds of fish aboard,” says Rozema. “They deliver great performance for that area. If you need to get somewhere, you have the power you need.”
Looking after the needs of fishermen, North American boatbuilders, engineers and designers continue to up the game in every aspect of boatbuilding, from safety to efficiency to productivity.