Processing fish at sea ranges from simple gutting on the deck of a traditional trawler to processing and packing traceable seafood ready for shipping on a Bering Sea freezer trawler like the Arctic Fjord, now in its first season in Alaska’s rich waters.
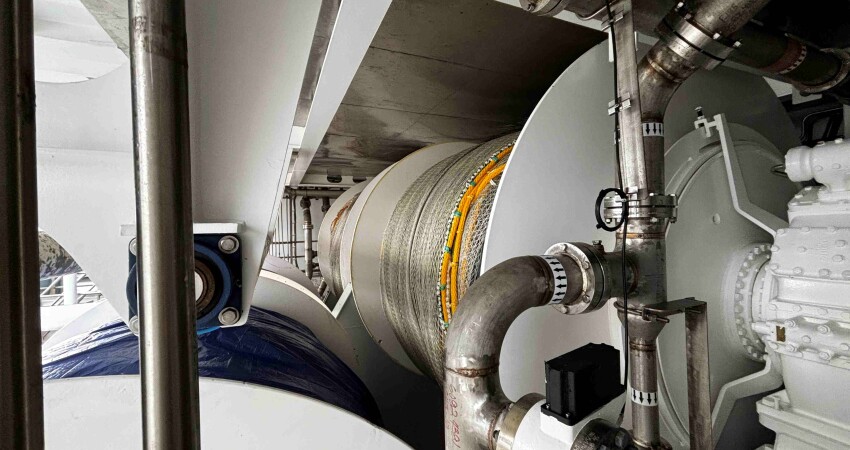
The 324-foot Arctic Fjord commences its precise processing operation by efficiently getting fish aboard. A crewman skillfully operates the winches on the bridge high above the deck while five men expertly handle the gear. “The low-pressure hydraulic system powers everything,” says Johnson. “There are ten hydraulic pumps, each with a 250-hp motor.” The trawl winches, manufactured by Rolls Royce, with 75-ton line pull, and according to Johnson, once the Thyborøn trawl doors are hung on the stern, one of the net reels takes the strain. “There’s four 27 cubic meter net reels—low pressure motors as well. They’re at the front end of the main trawl deck.”
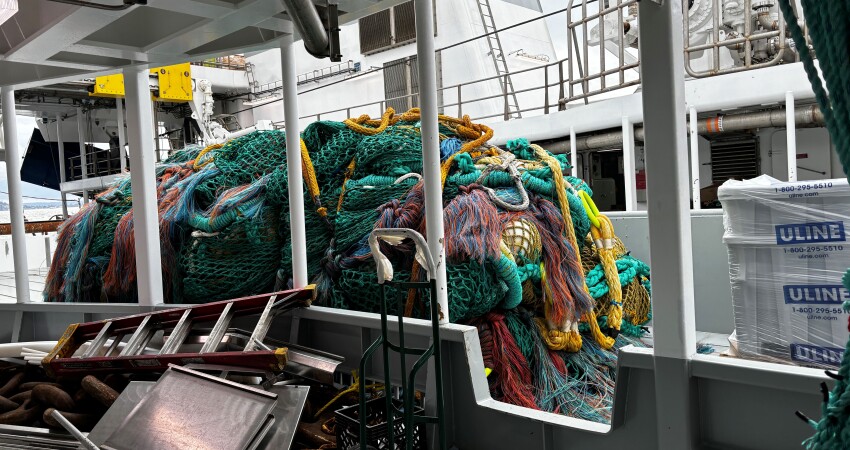
Once the net is reeled in and the cod end reaches the stern, Johnson explains, they use two Gilson winches to start hauling it aboard. “There are two D-rings on the cod end, and we’ll hook them onto. Once the cod end it aboard, it runs the length of the deck and is about 15 feet wide.” Johnson notes that the cod end might hold anywhere from 100 to 170 thousand pounds of fish.
“There are two cod end winches at the back, and they’ll hook onto the same D-rings and tight line the cod end between them and the Wilsons.” As Johnson describes it, the deckhands close the gate, unzip the cod end, open the live tank hatches on deck, and with the D-rings on the cod end held between the forward and aft winches, they slowly pull the cod end back and squeeze the catch out into the live tanks.
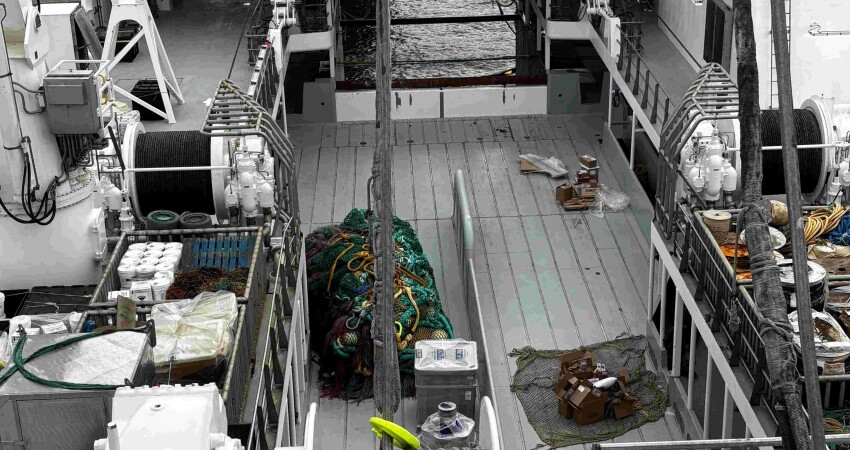
Once the fish are below, the factory starts processing. “Everything from the butchering to the case-up is consistent with what we already do,” says Johnson. “We designed the system. We worked with Carsoe on it, but our design is the process flow, particularly the surimi flow. We have a reputation for some of the highest quality surimi in the world, so it was important for us to maintain that. Besides surimi, Johnson notes that the new Arctic Fjord will process all the same products as the old Arctic Fjord, including fillets, roe, mince, meal, and oil. “We were decanting oil on the old boat,” he says. “But we burned it with the fuel because we didn’t have storage for it, but now we’re going to sell it for the first time.”
Below deck, the fish are lifted onto a conveyor belt that runs them across a flow scale. “That’s where you have the National Marine Fisheries Service observer.” From there the fish are sorted according to size, and product, and conveyed towards the appropriate processing lines.
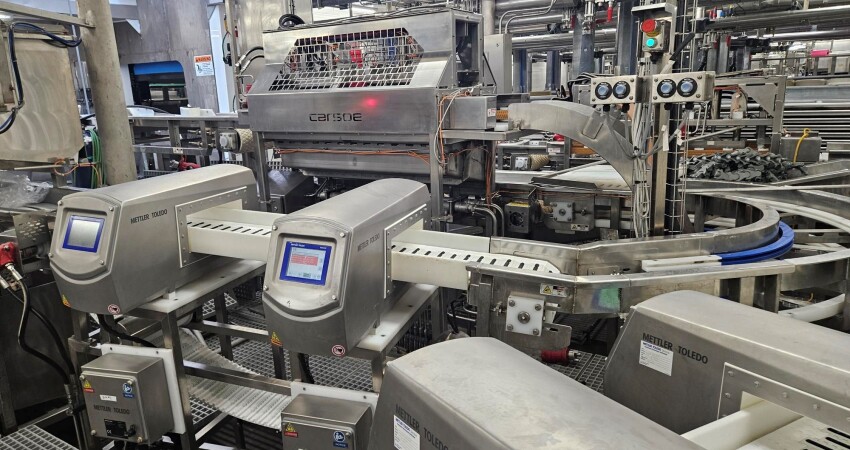
“The case-up, hotel, and palletizing system is where things have changed for us. That’s all new technology,” says Johnson. “We box our 10-kilo fillet blocks in standard-size cartons. They’re a commodity. But we have a slightly different size box for our surimi, so they fit the pallet better.” There are three hotels for surimi products, Johnson points out, where cases accumulate until they can fill a pallet. At that point, the fully automated system pulls the product out of the hotel to make up a pallet that will go into the freezer hold.

As an MSC-certified fishery, all the products on board must be traceable. Johnson notes that so far, the company has traced a lot, which is the entire product output from a trip. “This system will give us traceability by the hour if we want it,” he says. “We use Marel’s Inova software to manage our data. A QR code goes on each case and contains all the information on the case. Each case gets a serial number from Inova during case-up, and we’ll also have an inventory on the pallet tag.”
Johnson points out that the Carsoe automated palletizing and product handling system eliminates the need to handle 120 thousand 55-pound boxes and makes unloading faster and easier. “The boat will fill up in 12 to 20 days, and then we’ll turn around at Dutch Harbor. And a big part of this is to eliminate all that handling—which is a chance to damage boxes—and take that load off the crew.
Johnson reports that the boat is fishing well this first season, and the factory and automated systems are running as designed.